PaulM2
In the Brooder
- Feb 26, 2017
- 12
- 0
- 14
This is great thanks, and I intend to copy it, and have found a 12v motor with a 0,6 revolution on ebay! I gather that most egg turners, of the egg in a plastic holder type, turn the egg 40 degrees to either side making a total of 80 degrees. I have attached a sketch I have drawn to calculate where to drill the holes if I make a 3" (76mm) cam for this motor . I have put two holes which hold the connecting rod from the cam to the tray (omitted in the drawing for clarity). The holes need to be 2,9" (74mm) from the centre of the trays. I also put the limit stops on the cams that are exactly 90 degrees to the holes, (although in reality one can adjust the microswitches to suit where one made the holes. 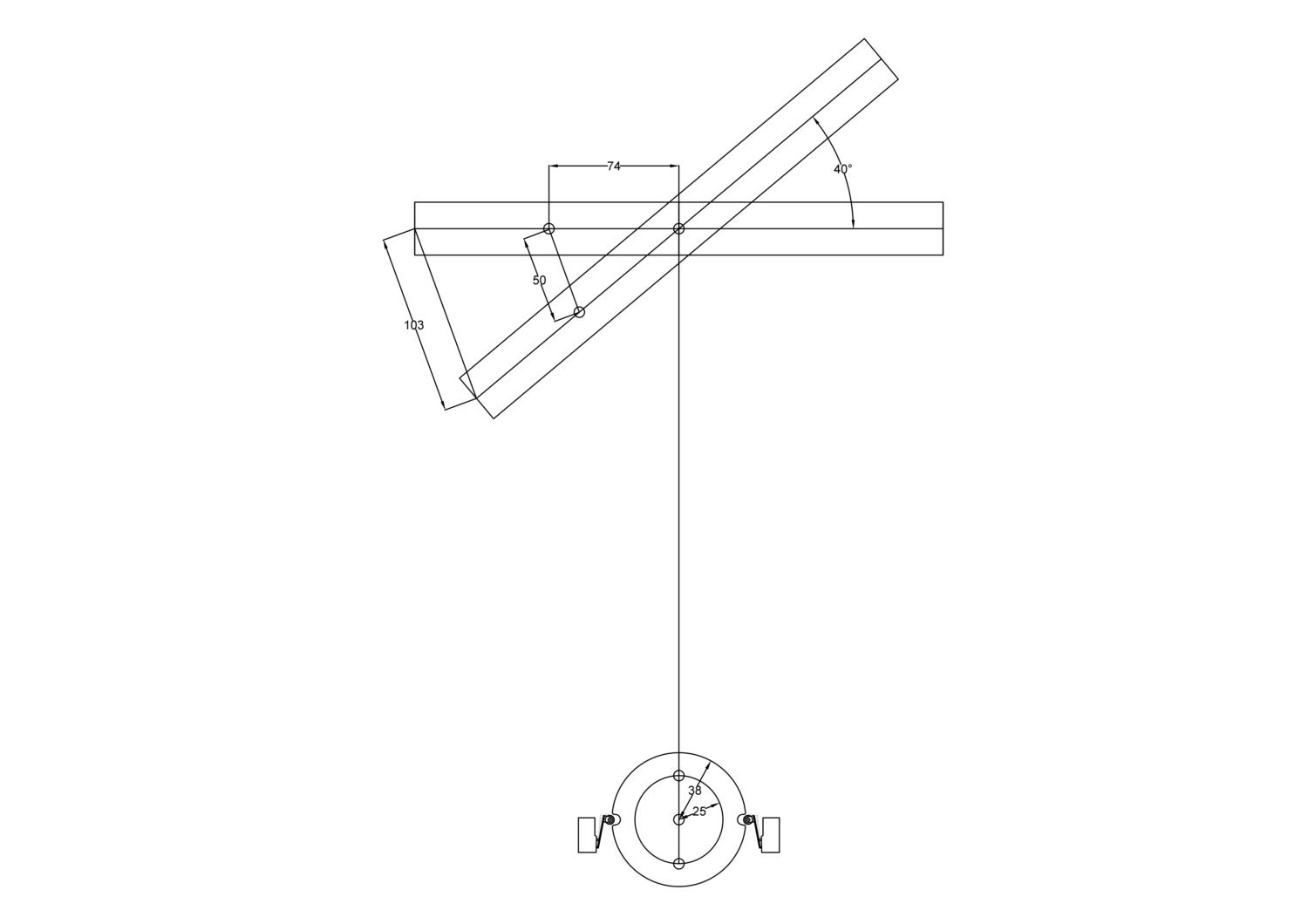
Last edited: