- Jun 2, 2013
- 3
- 0
- 7
I got a lot of ideas from you folks so I thought I would share my project with you. I have been keeping/raising chickens for over 13 years now. I've hatched with the Little Giant several times with mixed results. I am no expert but I happened along a discarded Pepsi cooler so I thought it would be fun to make a mega-bator. In addition to pics, I'll give you links to the best prices I found for many of the components.
But first, here is a disclaimer: I am not an electrician or any sort of professional engineer. These pictures are for your entertainment purposes only. Though I have attempted to be safe in my construction, I do not warrant this design in any way shape or form. Any user of this information agrees to use it, if at all, at their own risk.
Here is the finished project:
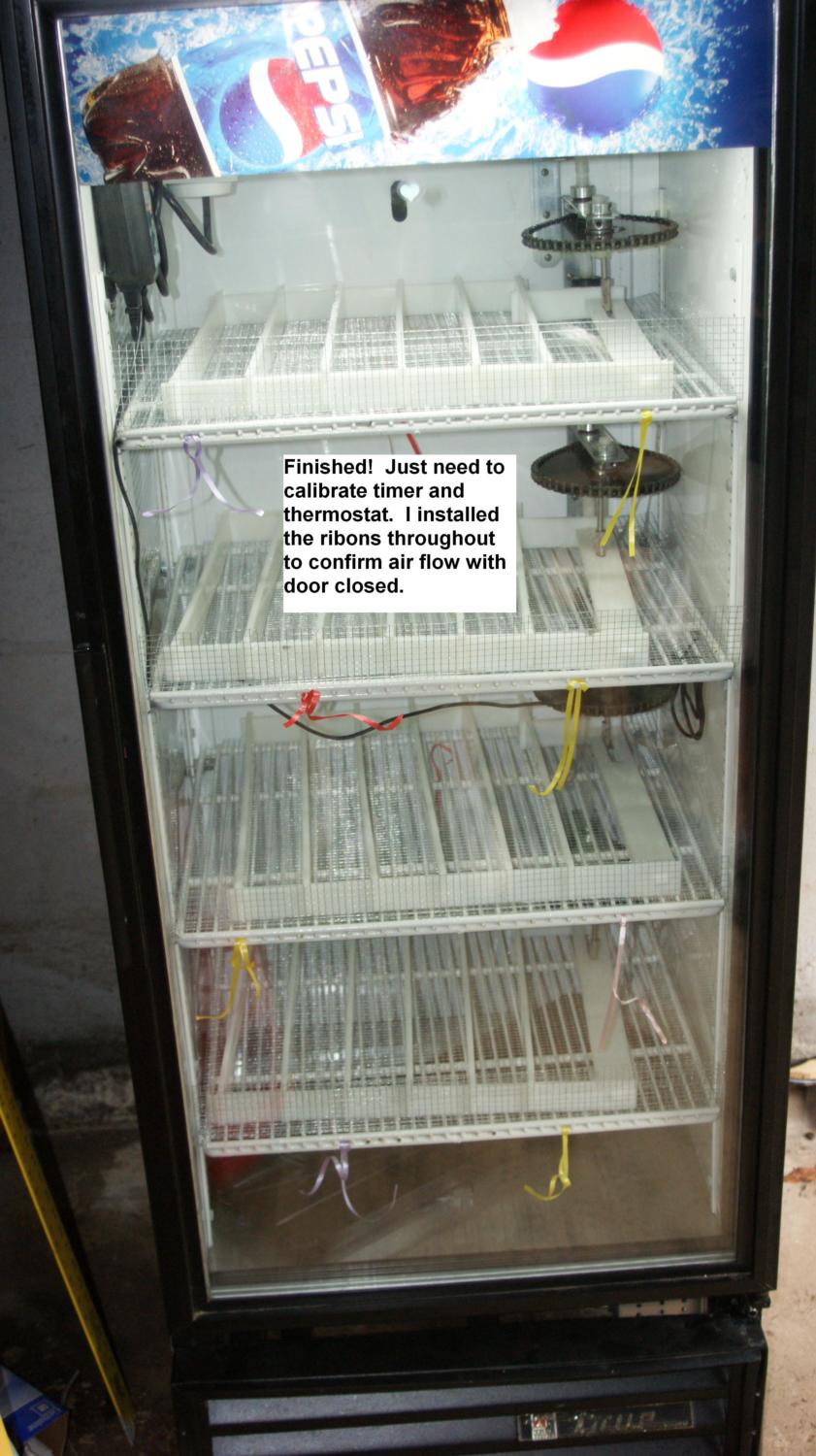
As you can see, I am using trays and a drive mechanism to move the eggs laterally in lieu of a rocking motion used in many designs. I figured rolling the eggs would be more like momma and would be easier to construct. I had an old outdoor grill rotisserie motor I used for the drive. I had a hard time finding inexpensive drive gears needed to gear down the speed. I calculated I wanted to move the eggs 3 inches every four hours. Essentially, the trays will move three inches one direction and then 3 inches back four hours later. Based on the motor speed I used a 10 tooth #35 drive sprocket chained to a 48 tooth sprocket. A slotted yoke attached to the tray provides the needed action.
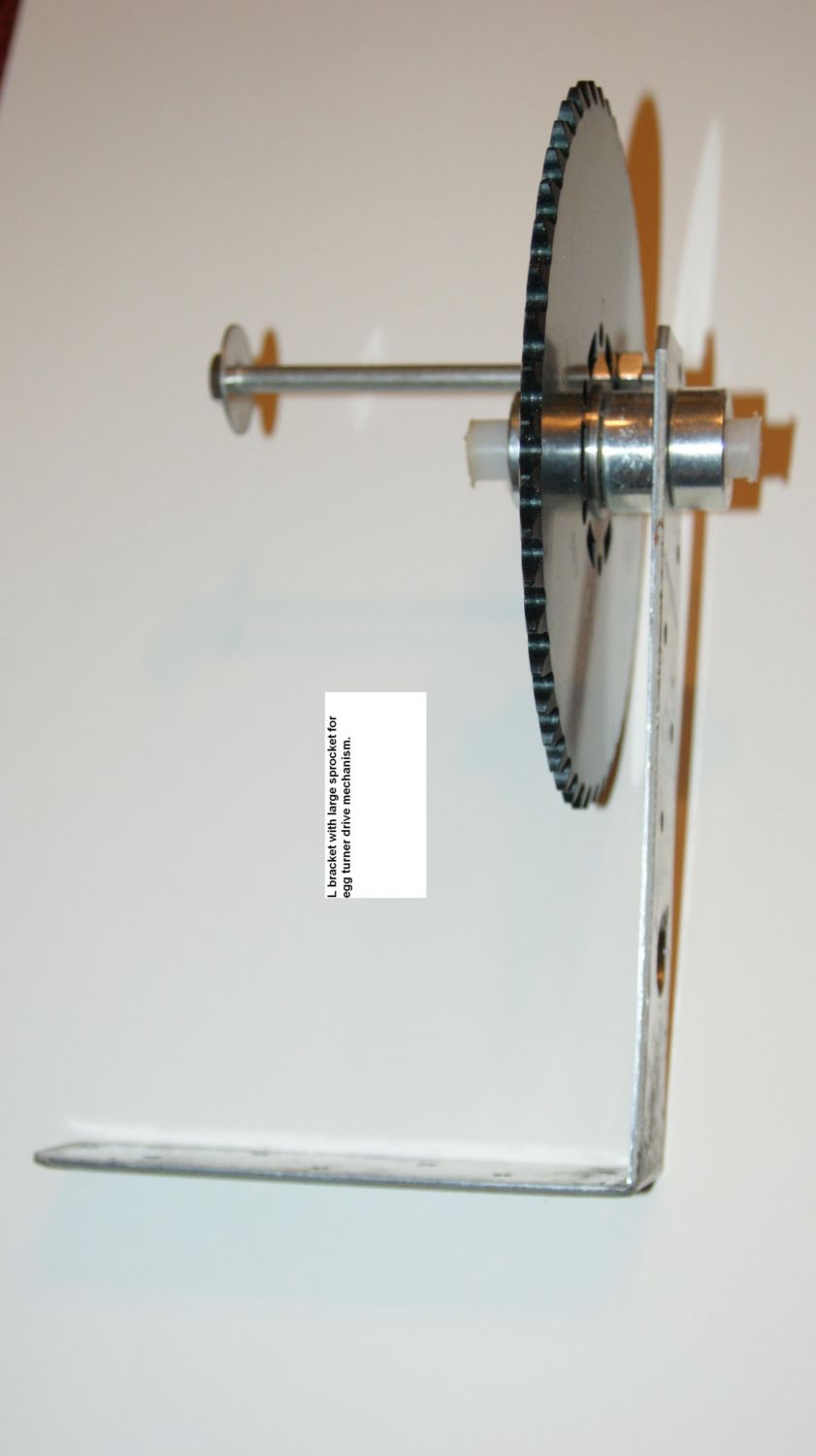
I could not locate an appropriate L bracket reasonably so I just bent 4 galvanized timber ties you can find at Lowes or Home Depot. Here is the best price I could find for the large sprocket, bearings, and chain: http://www.vexrobotics.com/vexpro/sprockets-and-chain/35-sprockets.html
The best price for the 10 tooth sprocket and other shaft rings, connectors and chain master links were found here:
http://www.rollerchain4less.com/35B10-12-Finished-Bore-Sprocket_p_509.html
I used high density polyethylene (HDPE) for the shaft and egg trays for sanitation and ease of use. Unfortunately, the tolerance on the 1/2" shaft required manual reduction on my part which was quite a hassle. I used a 24" X 48" 1/4" sheet for the egg trays. It was easy to cut with my table saw.
http://www.usplastic.com/catalog/item.aspx?itemid=33690&catid=705
http://www.usplastic.com/catalog/item.aspx?itemid=23869&catid=705
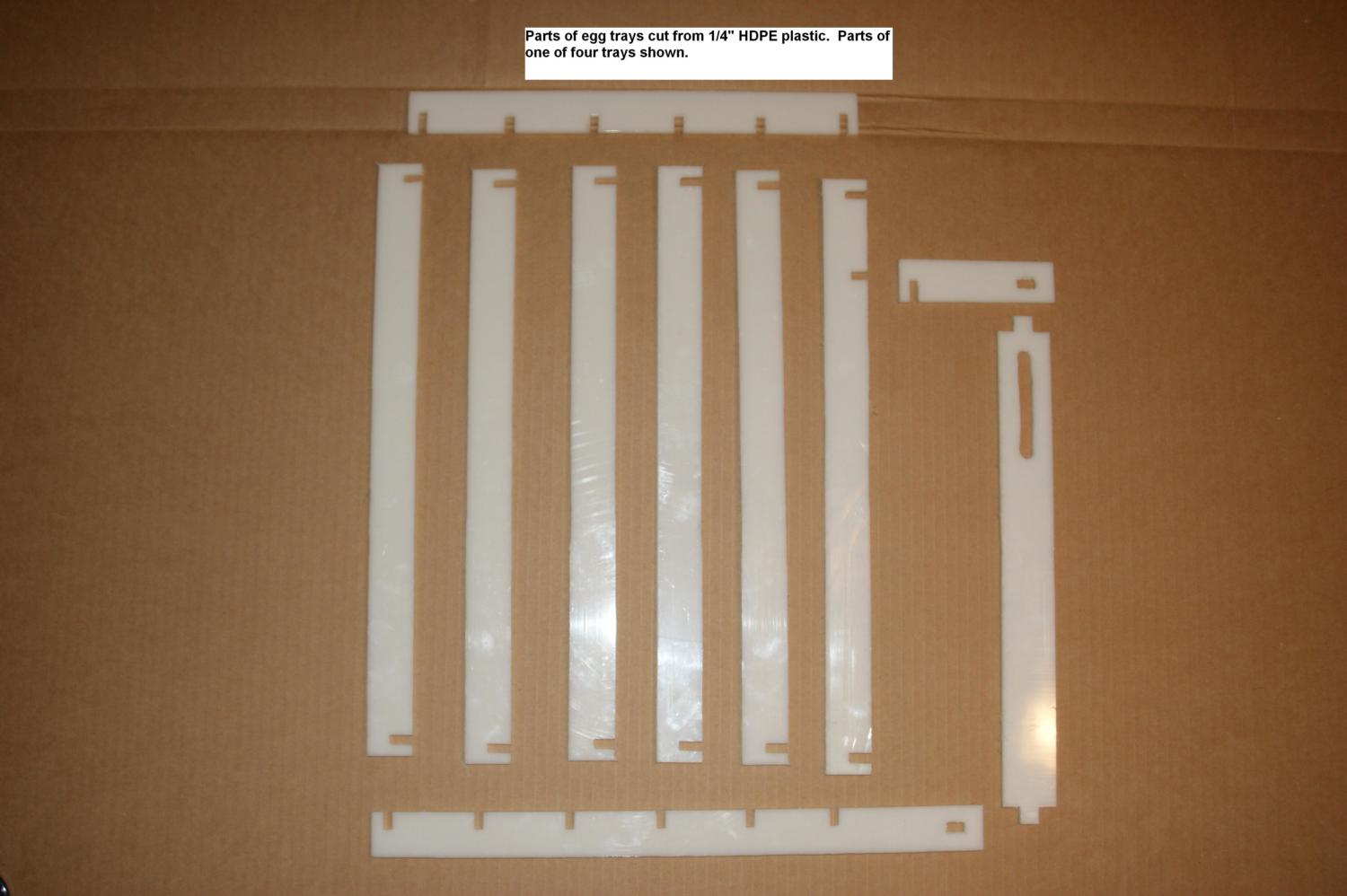
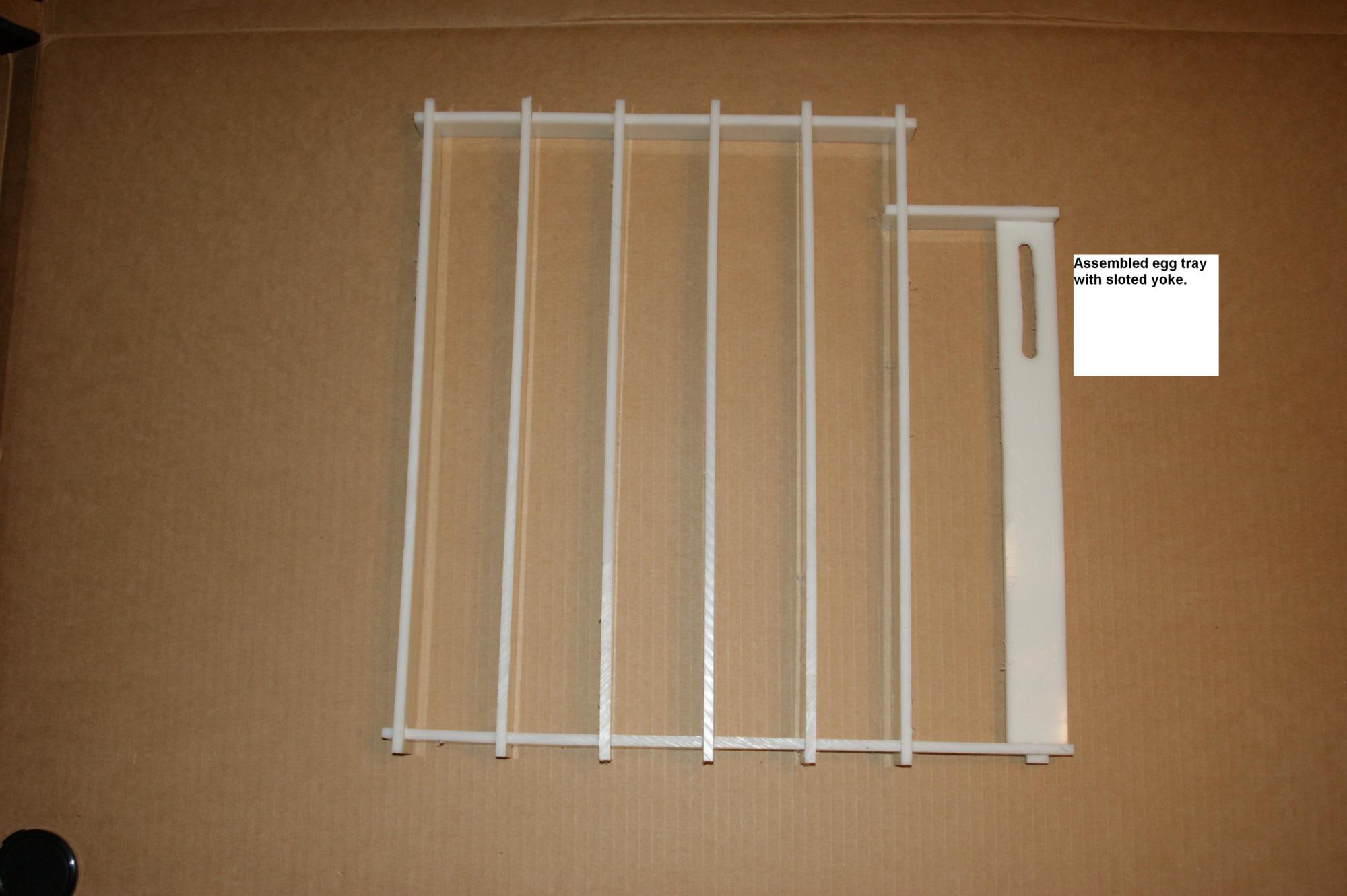
Here is the programmable timer for the turner:
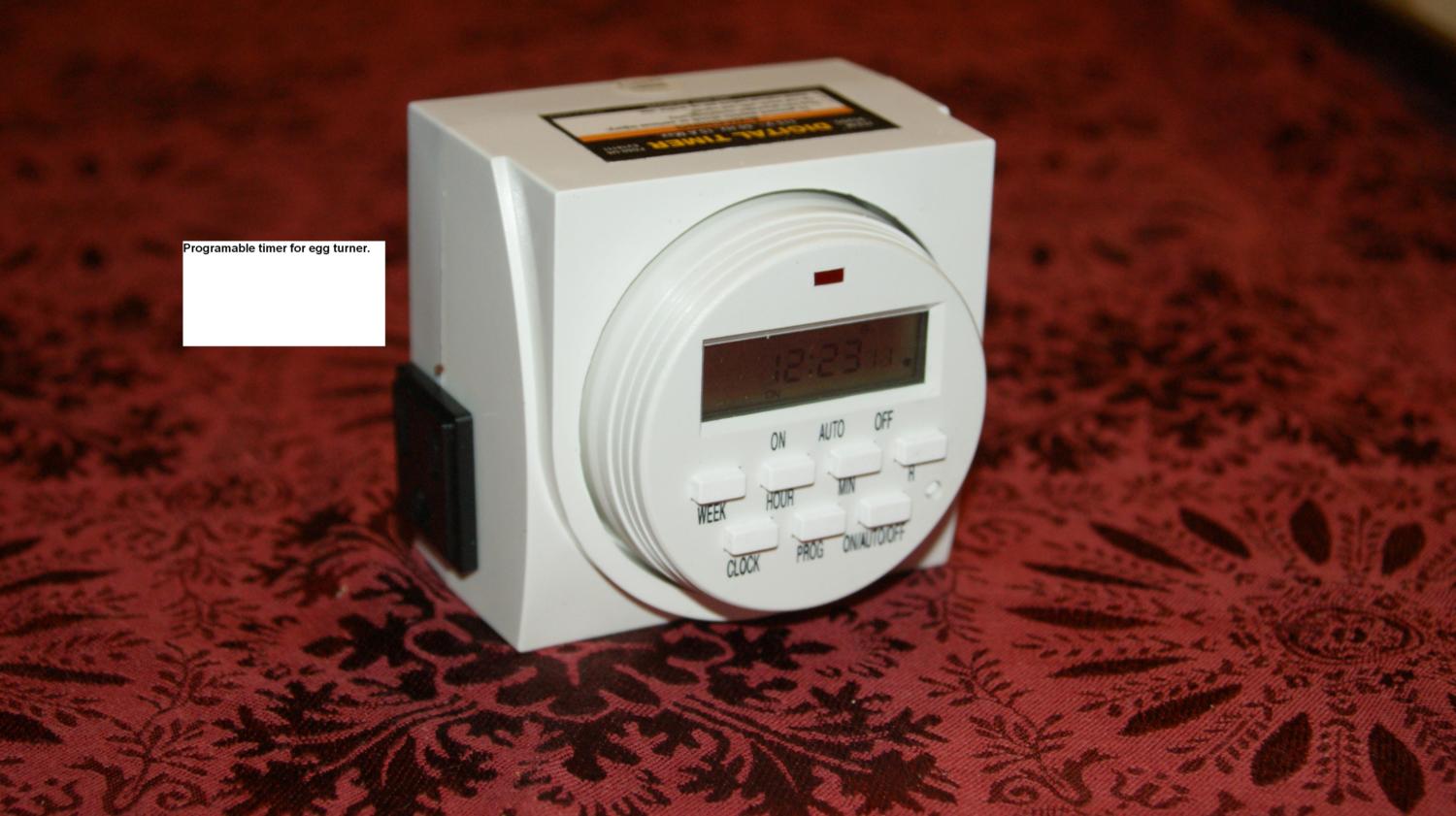
http://www.amazon.com/Hydrofarm-Dual-Outlet-Digital-Timer/dp/B001GBQ4F2/ref=pd_sbs_lg_5
I used four feet of 11" heat tape for the heating element. Along with the heat tape, the cord with clips, insulating tape, and aluminum tape were all very reasonable here: http://www.bigappleherp.com/Flex-Watt-Heat-Tape?gclid=CPOH7tyrsrUCFQdU4AodWhkAxQ

The heat tape is regulated by this thermostat which seems to have good reviews:
http://www.amazon.com/Hydrofarm-MTP...t-Heat/dp/B000NZZG3S/ref=cm_cr_pr_product_top

That about covers the major components, now a bit more about the build. It was easy to access the fan and temperature control so I thought it would be a good Idea to just replace the temperature control with a dimmer switch to the fan which makes the fan speed variable. I also installed a GFCI outlet to protect and power the heat tape and drive mechanism.


I removed the compressor and evaporator which probably cut the weight of the cooler in half. My original thought was to use the evaporator drip hose as the chase for the new power line for the heat tape and motor but it turned out that the chase in the back left corner that was used for the coolant lines was a better solution.
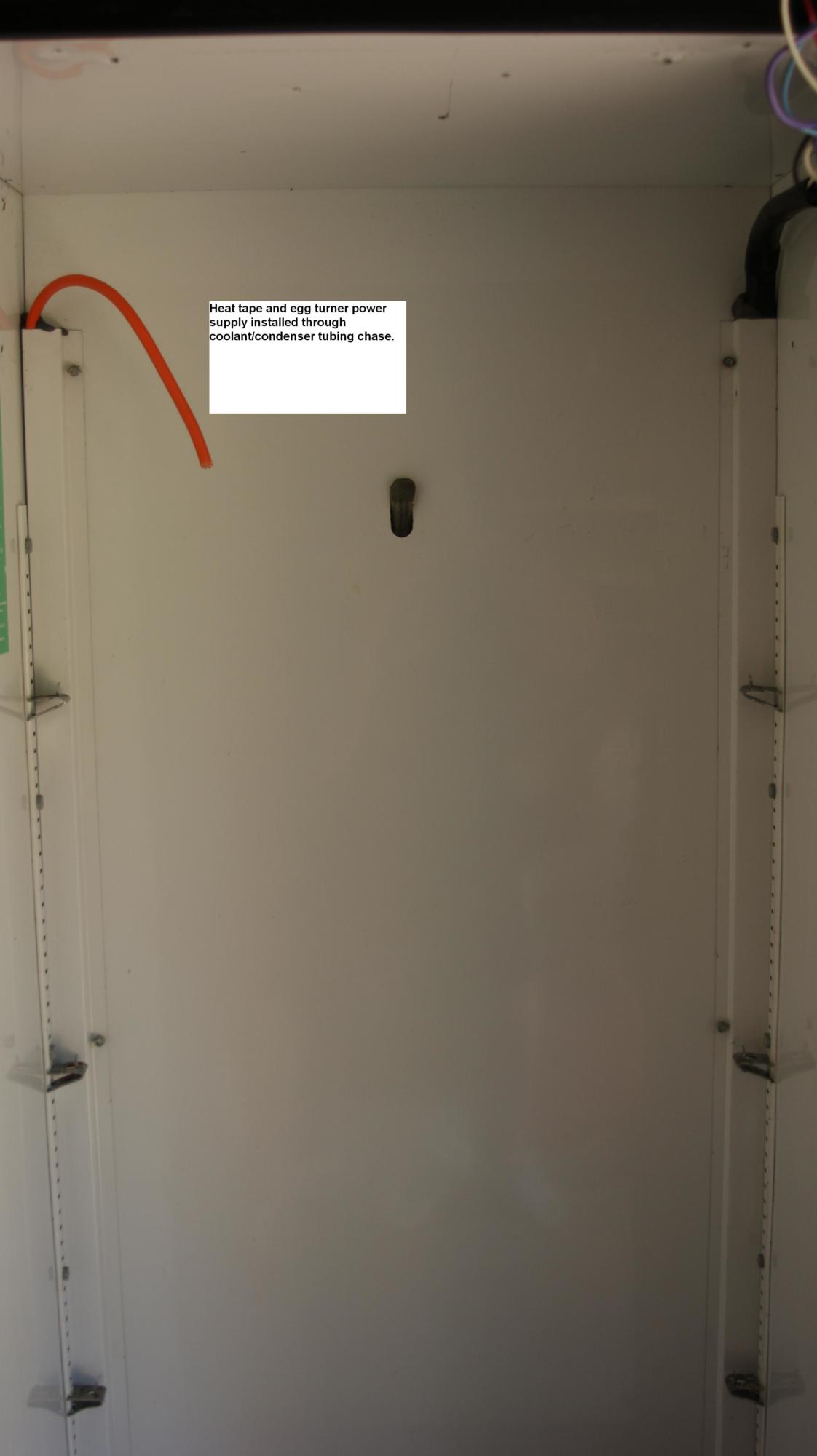
The fan sucked air up to the evaporator that sat behind the fan housing. In order to use the fan to circulate air throughout the incubator, I closed off the back of the fan with a sheet of aluminum flashing and I cut a slot in front of the fan to direct the air down along the door. I should probably put a screen across the slot opening to keep your fingers out
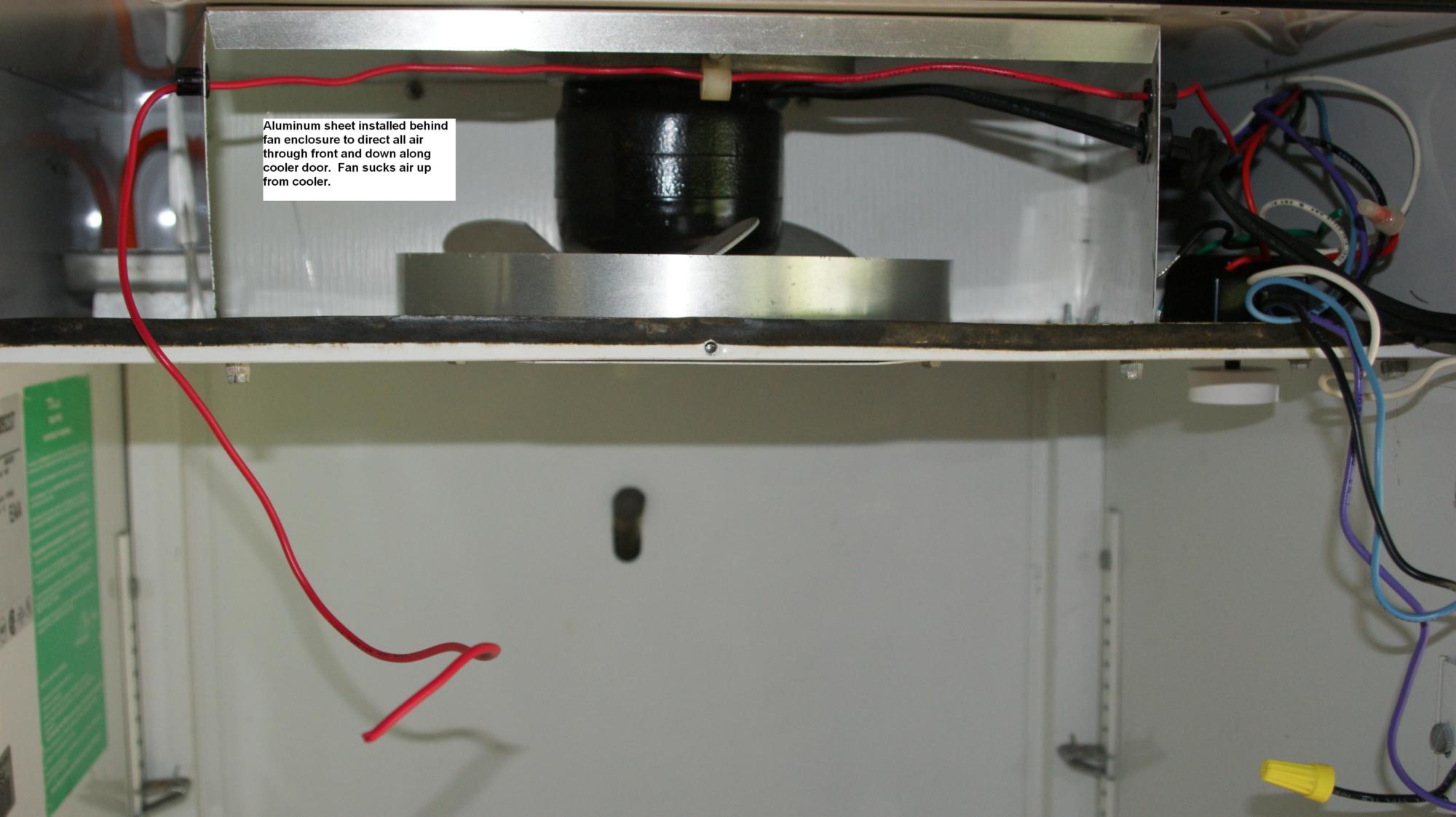
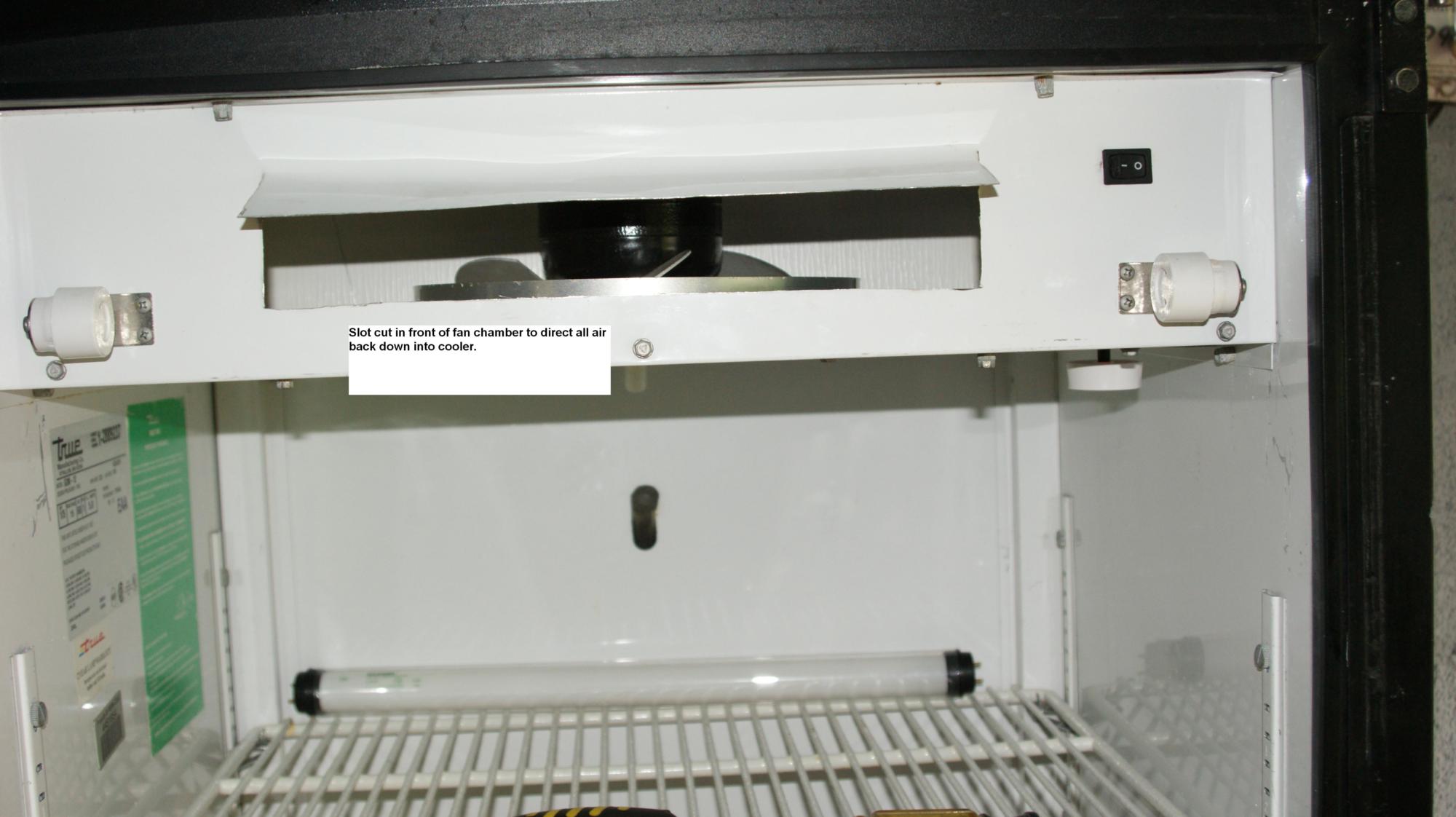
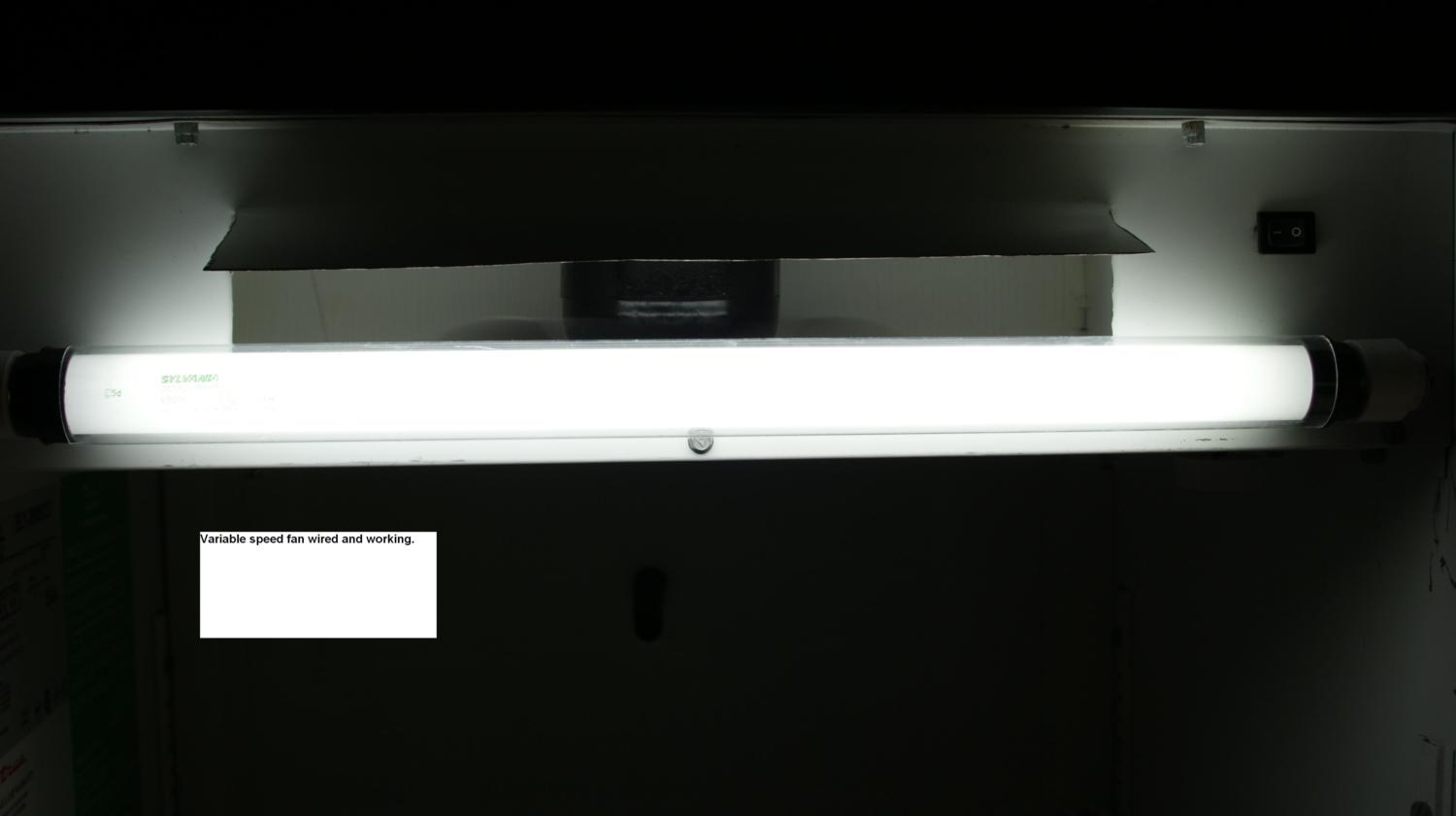
I toyed with the idea of installing some sort of tank to automatically fill the water pan, but I figured that wouldn't be worth the effort. I will be using the old drip pan in the bottom of the incubator.

Here the drive motor and large sprockets are installed:


Shelves, shaft and small sprockets and chains next.
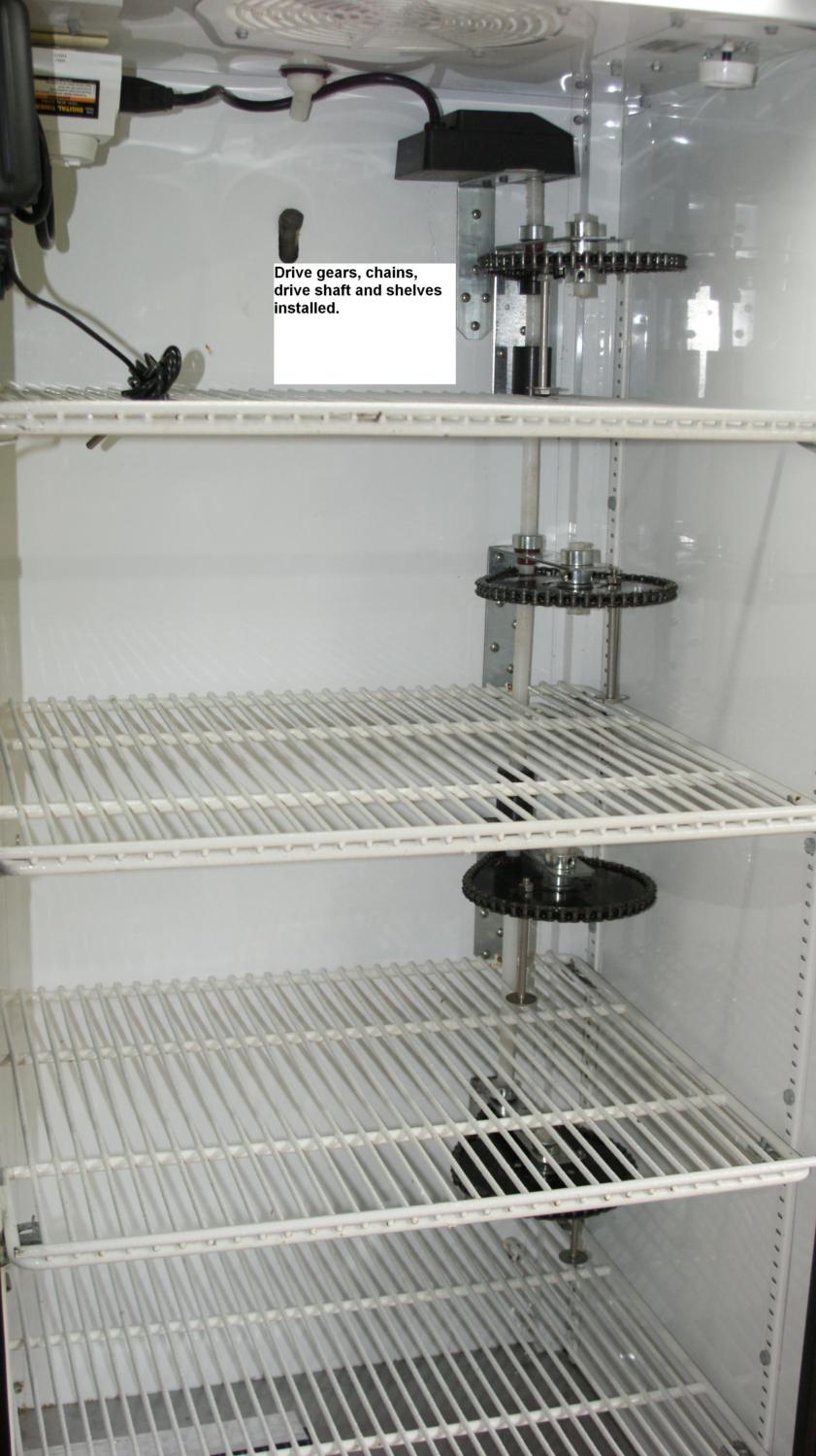
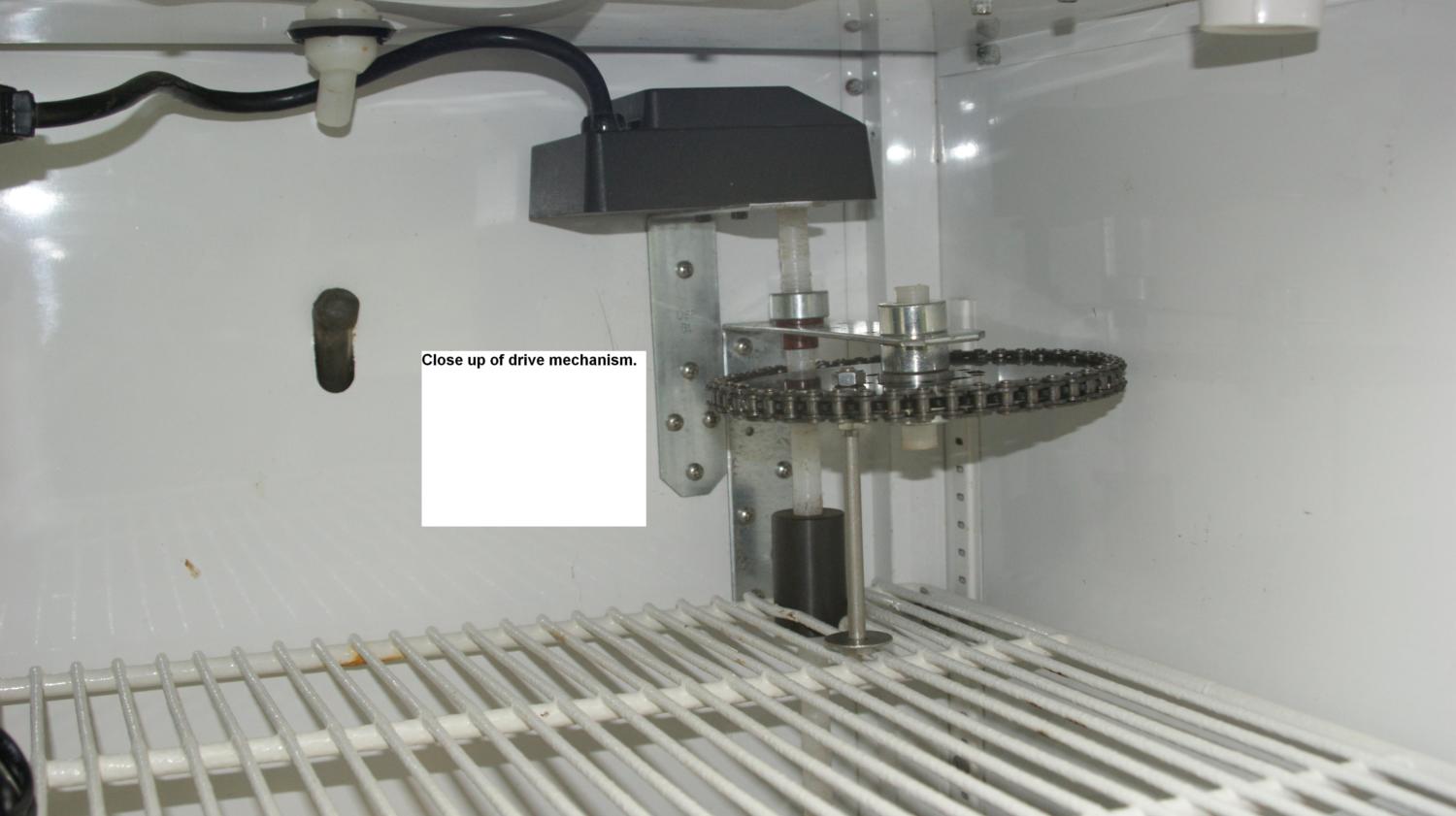
Here is the bottom showing the outdoor extension cord I used for the power line to the heat tape and drive motor GFCI outlet. The outlet shown here was originally for the compressor motor. I also re-wired to toggle switch to be the main switch for the whole machine.
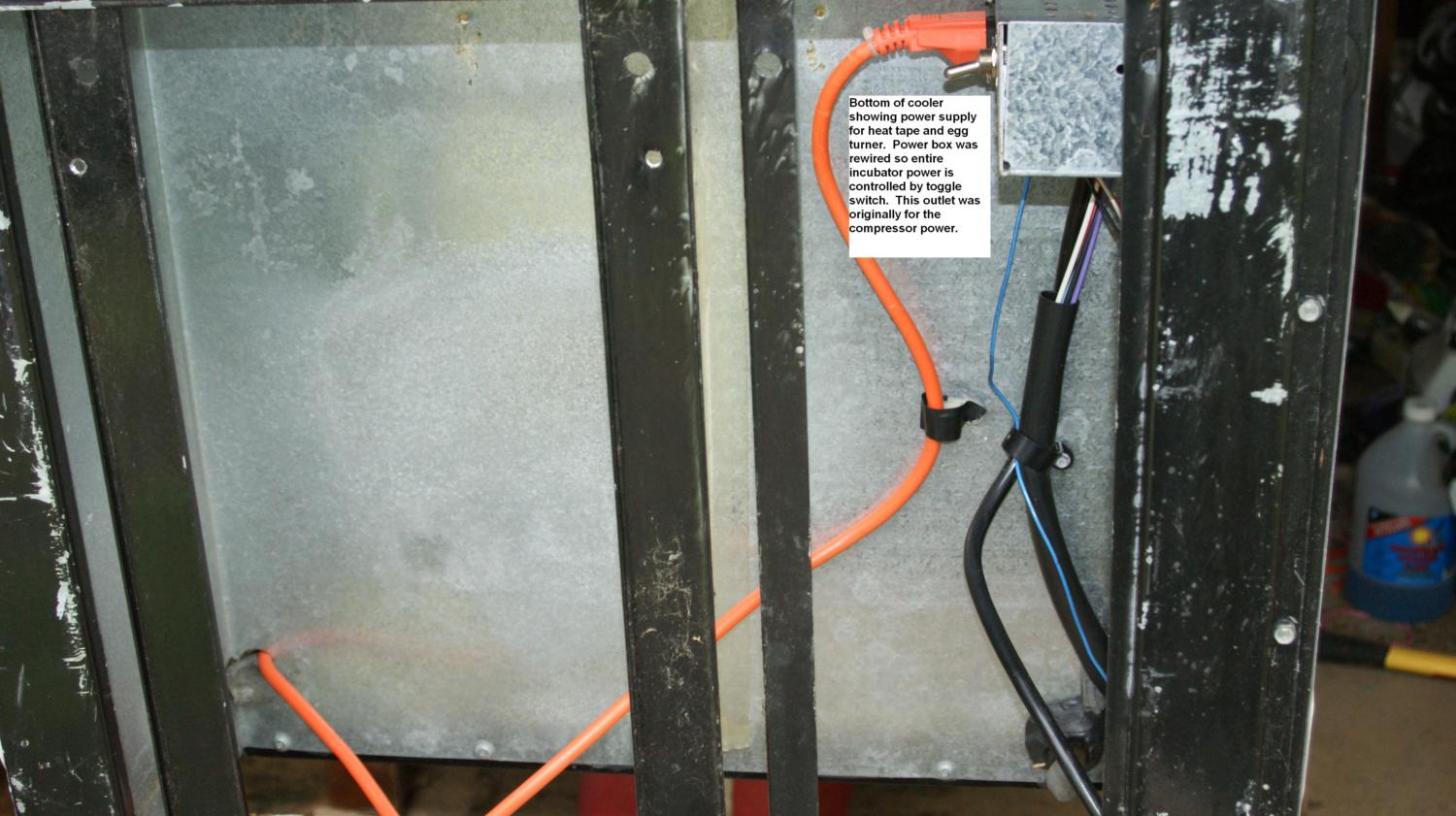
Here the trays are installed on top of 1/4" wire mesh with the slotted yolk attached to the drive train.
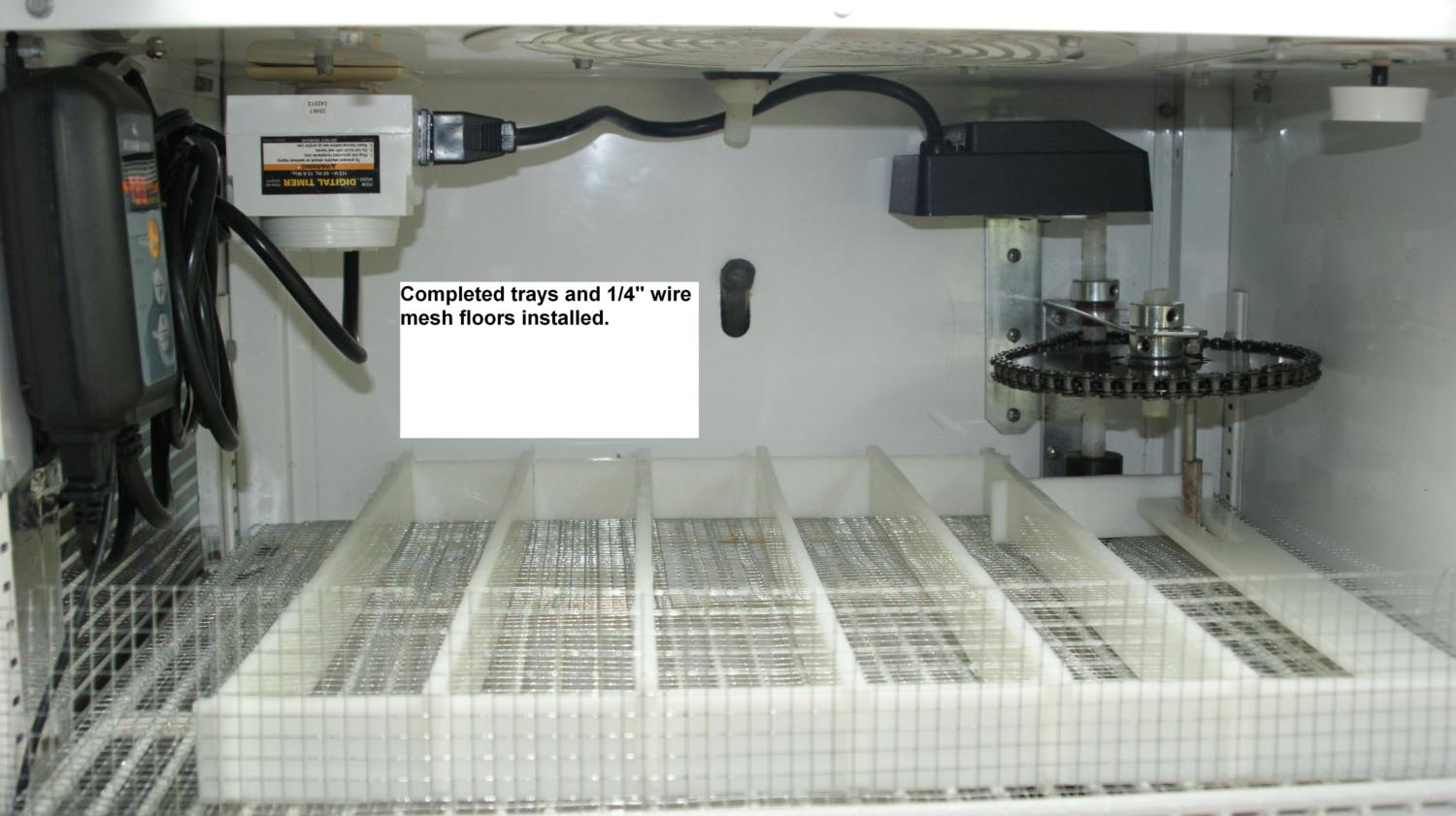
I used a 2.5" barrier at the front of each shelf to prevent the chicks from falling down the space between the shelves and the door.
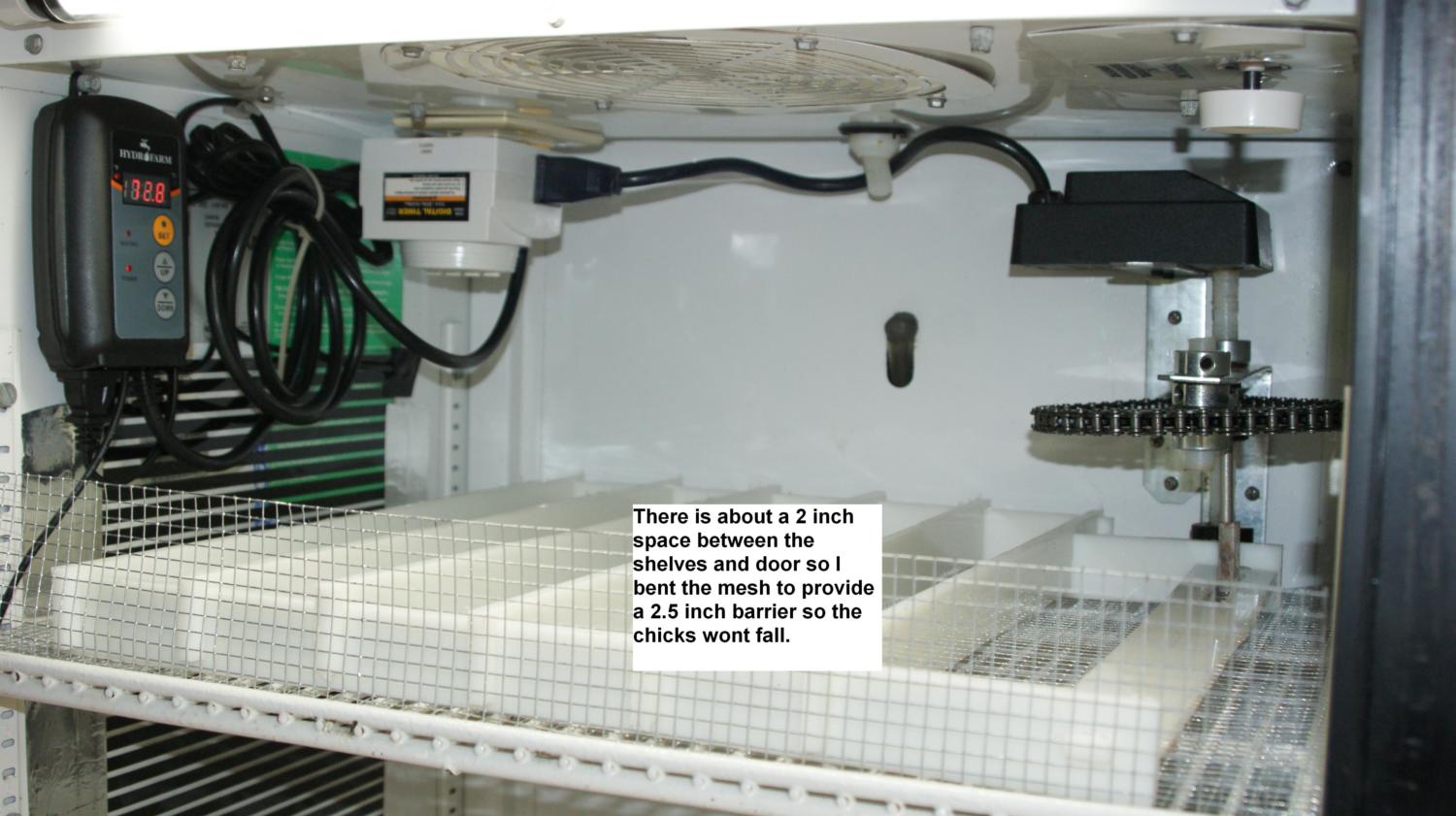
Well, I believe it will work, theoretically anyway. It is still warming up for its first time as I finish this. I will try to post updates, especially after the maiden hatch. Best Regards....
But first, here is a disclaimer: I am not an electrician or any sort of professional engineer. These pictures are for your entertainment purposes only. Though I have attempted to be safe in my construction, I do not warrant this design in any way shape or form. Any user of this information agrees to use it, if at all, at their own risk.
Here is the finished project:
As you can see, I am using trays and a drive mechanism to move the eggs laterally in lieu of a rocking motion used in many designs. I figured rolling the eggs would be more like momma and would be easier to construct. I had an old outdoor grill rotisserie motor I used for the drive. I had a hard time finding inexpensive drive gears needed to gear down the speed. I calculated I wanted to move the eggs 3 inches every four hours. Essentially, the trays will move three inches one direction and then 3 inches back four hours later. Based on the motor speed I used a 10 tooth #35 drive sprocket chained to a 48 tooth sprocket. A slotted yoke attached to the tray provides the needed action.
I could not locate an appropriate L bracket reasonably so I just bent 4 galvanized timber ties you can find at Lowes or Home Depot. Here is the best price I could find for the large sprocket, bearings, and chain: http://www.vexrobotics.com/vexpro/sprockets-and-chain/35-sprockets.html
The best price for the 10 tooth sprocket and other shaft rings, connectors and chain master links were found here:
http://www.rollerchain4less.com/35B10-12-Finished-Bore-Sprocket_p_509.html
I used high density polyethylene (HDPE) for the shaft and egg trays for sanitation and ease of use. Unfortunately, the tolerance on the 1/2" shaft required manual reduction on my part which was quite a hassle. I used a 24" X 48" 1/4" sheet for the egg trays. It was easy to cut with my table saw.
http://www.usplastic.com/catalog/item.aspx?itemid=33690&catid=705
http://www.usplastic.com/catalog/item.aspx?itemid=23869&catid=705
Here is the programmable timer for the turner:
http://www.amazon.com/Hydrofarm-Dual-Outlet-Digital-Timer/dp/B001GBQ4F2/ref=pd_sbs_lg_5
I used four feet of 11" heat tape for the heating element. Along with the heat tape, the cord with clips, insulating tape, and aluminum tape were all very reasonable here: http://www.bigappleherp.com/Flex-Watt-Heat-Tape?gclid=CPOH7tyrsrUCFQdU4AodWhkAxQ
The heat tape is regulated by this thermostat which seems to have good reviews:
http://www.amazon.com/Hydrofarm-MTP...t-Heat/dp/B000NZZG3S/ref=cm_cr_pr_product_top
That about covers the major components, now a bit more about the build. It was easy to access the fan and temperature control so I thought it would be a good Idea to just replace the temperature control with a dimmer switch to the fan which makes the fan speed variable. I also installed a GFCI outlet to protect and power the heat tape and drive mechanism.
I removed the compressor and evaporator which probably cut the weight of the cooler in half. My original thought was to use the evaporator drip hose as the chase for the new power line for the heat tape and motor but it turned out that the chase in the back left corner that was used for the coolant lines was a better solution.
The fan sucked air up to the evaporator that sat behind the fan housing. In order to use the fan to circulate air throughout the incubator, I closed off the back of the fan with a sheet of aluminum flashing and I cut a slot in front of the fan to direct the air down along the door. I should probably put a screen across the slot opening to keep your fingers out

I toyed with the idea of installing some sort of tank to automatically fill the water pan, but I figured that wouldn't be worth the effort. I will be using the old drip pan in the bottom of the incubator.
Here the drive motor and large sprockets are installed:
Shelves, shaft and small sprockets and chains next.
Here is the bottom showing the outdoor extension cord I used for the power line to the heat tape and drive motor GFCI outlet. The outlet shown here was originally for the compressor motor. I also re-wired to toggle switch to be the main switch for the whole machine.
Here the trays are installed on top of 1/4" wire mesh with the slotted yolk attached to the drive train.
I used a 2.5" barrier at the front of each shelf to prevent the chicks from falling down the space between the shelves and the door.
Well, I believe it will work, theoretically anyway. It is still warming up for its first time as I finish this. I will try to post updates, especially after the maiden hatch. Best Regards....
Last edited: