Wow! Nobody has been on or nobody wants to help?
I'll share my progress anyway... first, the inside: At the back, you see the drainage hole which will have the wiring run to the outside. At the front, top and center is a ventilation hole. Same thing left of the light bulb at the front. Then next to the light bulb is my fan directly in front of the recirculation vent.
As we speak, I have contracted a small piece of metal to run from the turner to both egg trays... I really hope this will work. For "mounting" the turner, I bought a blue plastic outlet box from the hardware store and cut it in half, length-wise. It made a great bracket. I had to cut a little away so the motor could be mounted correctly. I will get a close up shot or two of that if anybody wants it. My shelves are cut from flourescent light covers. The sheets are about 24x48 inches and a little less that 1/2" thick. The provide for great circulation and are strong enough to hold what will go onto them. To be sure though, I put screws underneath on the outside edge as well as one in the back to act as a shelf support. My two egg turner trays... I cut each of the pegs so that I could turn that part around to save space. This is a tight fit. I'm sure though, that it has enough room to do its job. I'll get close ups of that too if anyone needs clarity.
There is room down below for two large hatching baskets plus a smaller one on the very bottom. At the very bottom, you can see the air intake that I have put a filter into to catch dust. I can provide close ups of that as well.
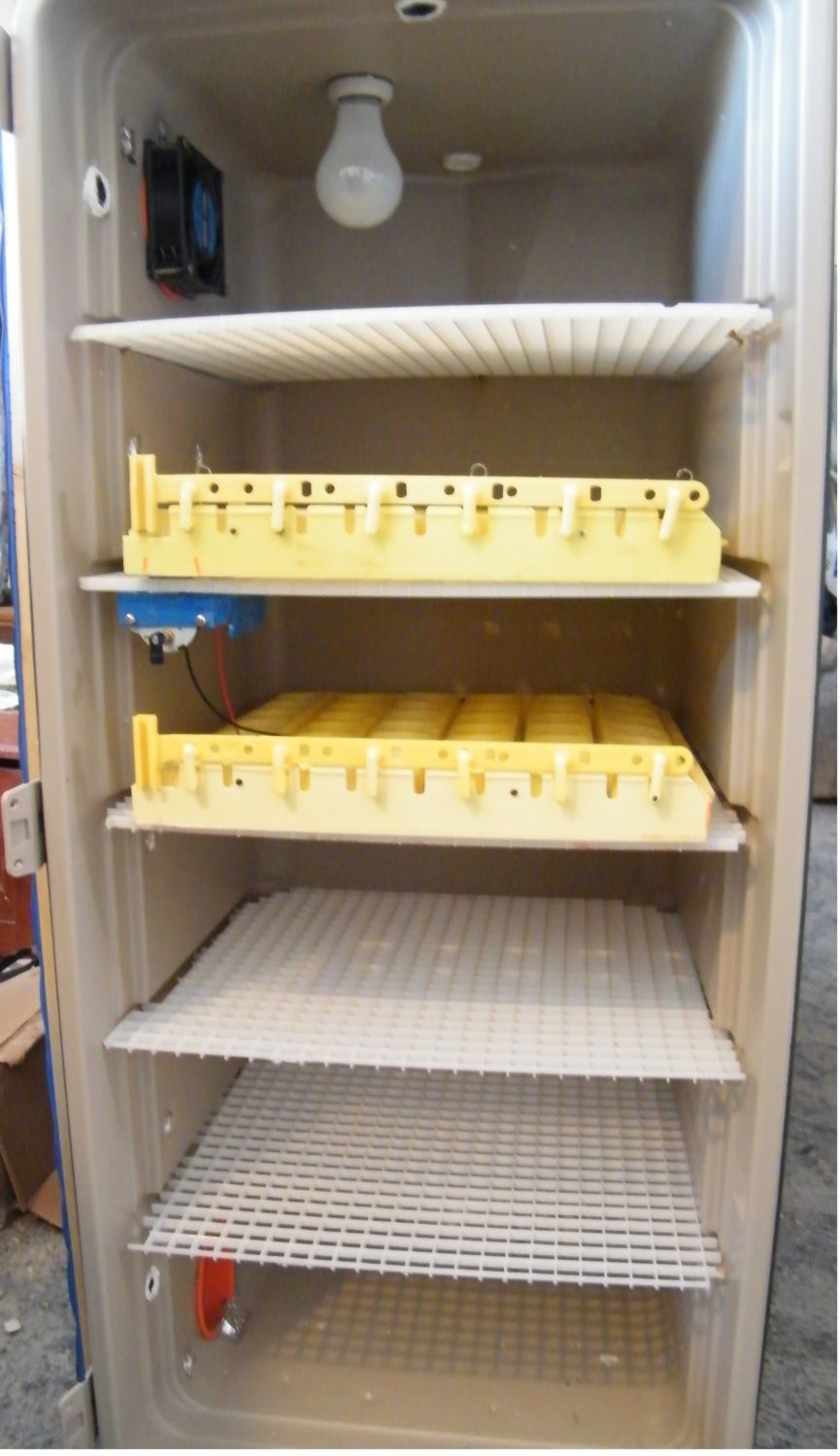
Edited to add: Look at the picture above. On the very bottom, I have drilled 16 1/4" holes for the carbon dioxide to exit, or is it carbon monoxide... whatever... they are there and hopefully, I won't have any issues regarding poisonous gases being given off and building up from the eggs themselves.
Now, back to your regularly scheduled program:
Through the door: I originally had my control center mounted in the center but there was too much insulation around it and so I moved it over. Now I need to plug the original hole and cover it up the best I can. Hopefully, I have a piece of the plastic from the big cut out center left to fill it with.
I cut strips from the big cut out piece to frame, support and secure the plexiglass to the outside. The sheet of plexiglass on the inside is secured with aluminum tape.
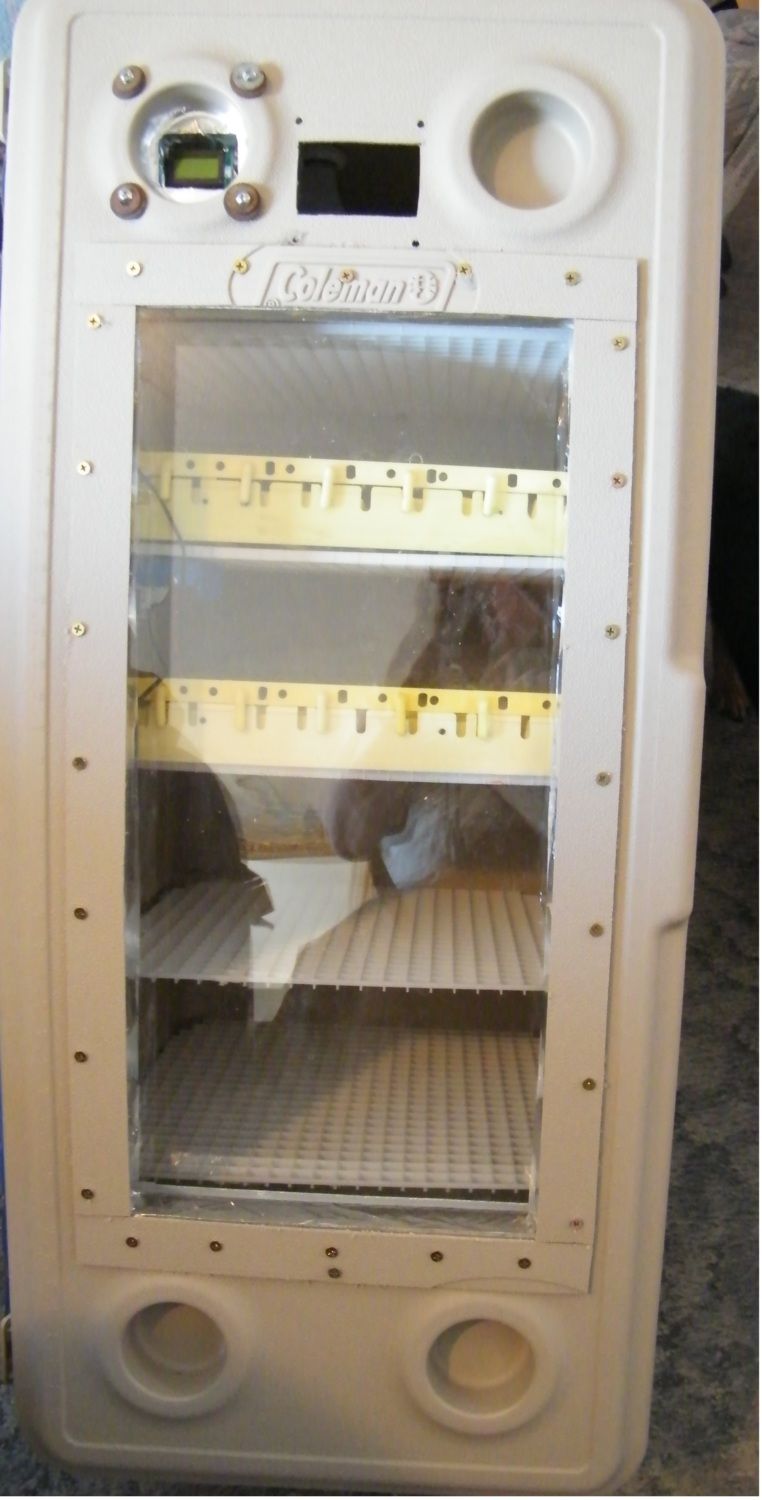
Recirculation Vent: I only had 1-1/2" of space along-side the cooler inside the cabinet so I used 1x2 furring strips to form my vent. I used two layers of blue foam from a cheapy exercise mat to insulate the vent. Then I covered it with aluminum flashing. I would have preferred a flatter edge but I couldn't do that without adding more and I just don't think I have the room for another layer of anything on there. It looks pretty lumpy but it is air tight. I will be putting some aluminum tape over the wood and over the edge as well to be sure no air leaks. There is a ventilation hole there at the top and bottom too. I cut 3/4" diameter holes and cut grey pipe to length. I caulked the edges inside and out with a silicone caulk that is mold proof. On the outside of the vents I have pieces of plastic canvas. I cannot tell you how many spiders I have had to remove from my incubators even though the holes on the outside are small. Hopefully the holes in the plastic canvas will keep them out. Hopefully, these vents will be sufficient. If not, I can cut more. It's a major pain in my backside as I have no drill for this and have to do it by hand. I also have to cut the grey pipe by hand and smooth the edges with a file. If I need more, somebody please say so and I'll get it done.

And my well protected Control Panel: at the bottom of a cup holder. It gets good air circulation as there is no insulation around it on the inside. I had to use two washers on the bolts as I couldn't find bolts the correct width and have them be the correct length too so ... old washers I had on hand.
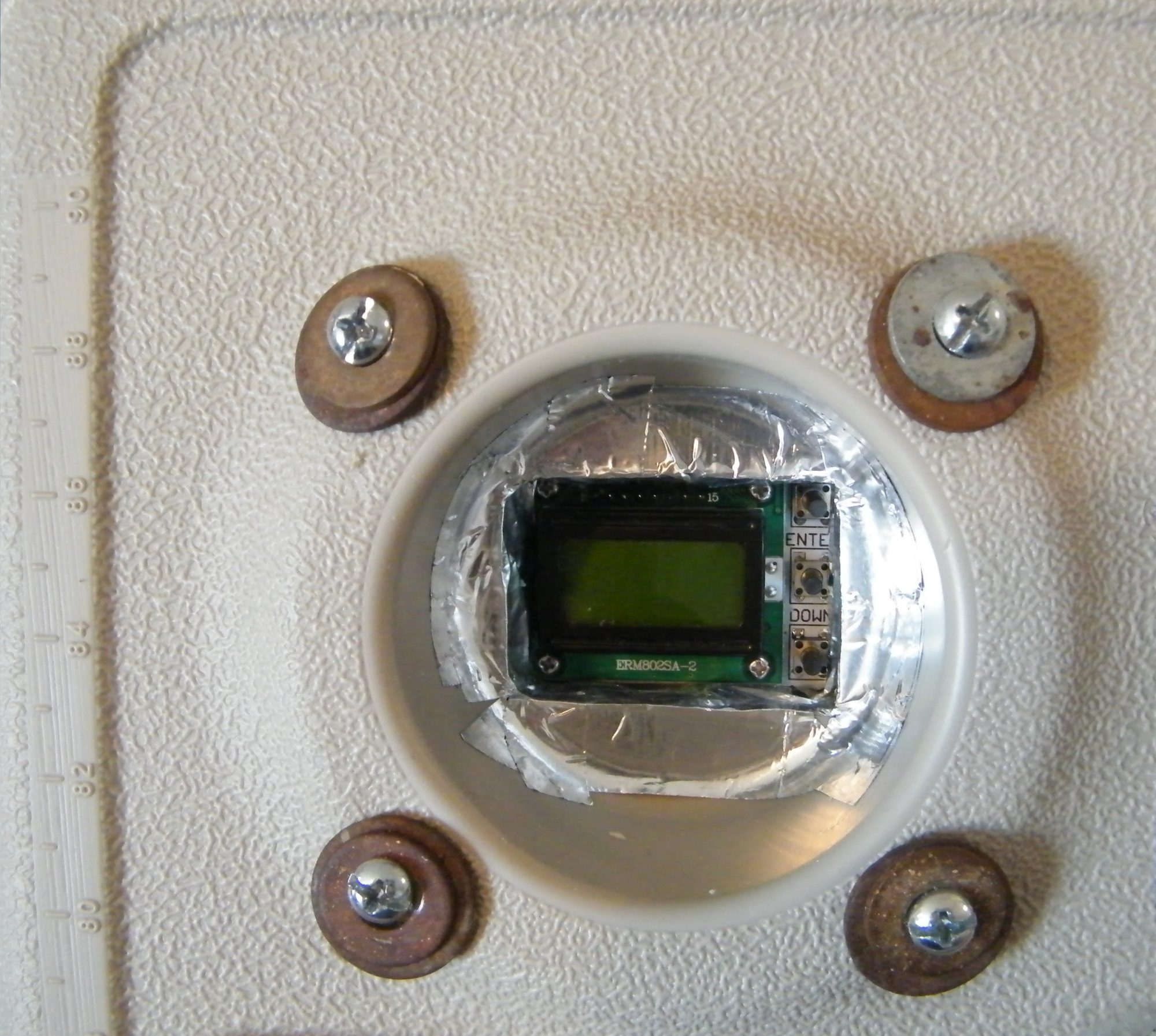
I have the wood addition on the cabinet sanded and stained and it looks pretty good. With exception to the black screw heads, you can almost not tell that anything was added... it's ok though, I don't mind the way it looks. I'll get a picture of it soon. Right now it's outside covered in plastic to protect it from the rain we got last week.
I'll share my progress anyway... first, the inside: At the back, you see the drainage hole which will have the wiring run to the outside. At the front, top and center is a ventilation hole. Same thing left of the light bulb at the front. Then next to the light bulb is my fan directly in front of the recirculation vent.
As we speak, I have contracted a small piece of metal to run from the turner to both egg trays... I really hope this will work. For "mounting" the turner, I bought a blue plastic outlet box from the hardware store and cut it in half, length-wise. It made a great bracket. I had to cut a little away so the motor could be mounted correctly. I will get a close up shot or two of that if anybody wants it. My shelves are cut from flourescent light covers. The sheets are about 24x48 inches and a little less that 1/2" thick. The provide for great circulation and are strong enough to hold what will go onto them. To be sure though, I put screws underneath on the outside edge as well as one in the back to act as a shelf support. My two egg turner trays... I cut each of the pegs so that I could turn that part around to save space. This is a tight fit. I'm sure though, that it has enough room to do its job. I'll get close ups of that too if anyone needs clarity.
There is room down below for two large hatching baskets plus a smaller one on the very bottom. At the very bottom, you can see the air intake that I have put a filter into to catch dust. I can provide close ups of that as well.
Edited to add: Look at the picture above. On the very bottom, I have drilled 16 1/4" holes for the carbon dioxide to exit, or is it carbon monoxide... whatever... they are there and hopefully, I won't have any issues regarding poisonous gases being given off and building up from the eggs themselves.
Now, back to your regularly scheduled program:
Through the door: I originally had my control center mounted in the center but there was too much insulation around it and so I moved it over. Now I need to plug the original hole and cover it up the best I can. Hopefully, I have a piece of the plastic from the big cut out center left to fill it with.
I cut strips from the big cut out piece to frame, support and secure the plexiglass to the outside. The sheet of plexiglass on the inside is secured with aluminum tape.
Recirculation Vent: I only had 1-1/2" of space along-side the cooler inside the cabinet so I used 1x2 furring strips to form my vent. I used two layers of blue foam from a cheapy exercise mat to insulate the vent. Then I covered it with aluminum flashing. I would have preferred a flatter edge but I couldn't do that without adding more and I just don't think I have the room for another layer of anything on there. It looks pretty lumpy but it is air tight. I will be putting some aluminum tape over the wood and over the edge as well to be sure no air leaks. There is a ventilation hole there at the top and bottom too. I cut 3/4" diameter holes and cut grey pipe to length. I caulked the edges inside and out with a silicone caulk that is mold proof. On the outside of the vents I have pieces of plastic canvas. I cannot tell you how many spiders I have had to remove from my incubators even though the holes on the outside are small. Hopefully the holes in the plastic canvas will keep them out. Hopefully, these vents will be sufficient. If not, I can cut more. It's a major pain in my backside as I have no drill for this and have to do it by hand. I also have to cut the grey pipe by hand and smooth the edges with a file. If I need more, somebody please say so and I'll get it done.
And my well protected Control Panel: at the bottom of a cup holder. It gets good air circulation as there is no insulation around it on the inside. I had to use two washers on the bolts as I couldn't find bolts the correct width and have them be the correct length too so ... old washers I had on hand.
I have the wood addition on the cabinet sanded and stained and it looks pretty good. With exception to the black screw heads, you can almost not tell that anything was added... it's ok though, I don't mind the way it looks. I'll get a picture of it soon. Right now it's outside covered in plastic to protect it from the rain we got last week.
Last edited: