So when you shell out $400 for a brand new steel milking stand with all the works, you should expect to receive a flawless piece of work, right? Right?!
Apparently, this is not the case in my case. Yep, I hemorrhaged all that money expecting a nice, function stand. But one critical defect has rendered it useless. I'm a little steamed, to say the least.Working with metal is NOT my strong point. But considering that it would cost me at least $100 to send this very heavy stand back, I guess a DIY fix is required.
Here are the pictures. That is a square pocket that is severely deformed out of shape.
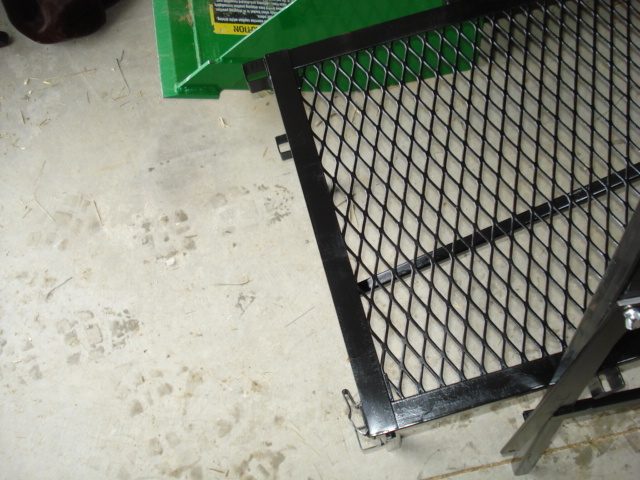



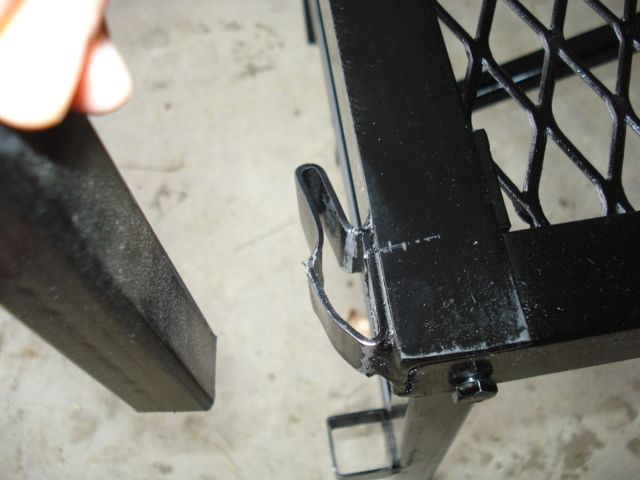
Because it is the slot where the headgate for the milking stand fits into it, I can't use the headgate without that square pocket! Without the headgate to secure my fidgety first freshener, the stand is, at most, a nice platform with a ramp. I wouldn't be so mad if it was a square pocket for one of the side rails, but yea, no, it had to be the headgate.
The UPS driver delivered the package very carefully. The man listened to the directions to lay the package flat with the marked side up (I was there to receive it personally). I transported it by sled, flat with that marked side up, to the tractor shed. I only unboxed it today (got it this past Thursday, but I was busy until now). Now I am kicking myself. I already cut apart the box, too, which was a derp move.
How can I fix this? How can I make it functional? What should I tell the seller? I am trying not to compose a "thanks for the crap" email. I will have to cool off a bit. I bought this stand because it was made in the U.S.A., and had good reviews backing it up. The seller did take much longer than originally estimated to ship to to me, but if orders are busy, they I can understand.
Apparently, this is not the case in my case. Yep, I hemorrhaged all that money expecting a nice, function stand. But one critical defect has rendered it useless. I'm a little steamed, to say the least.Working with metal is NOT my strong point. But considering that it would cost me at least $100 to send this very heavy stand back, I guess a DIY fix is required.
Here are the pictures. That is a square pocket that is severely deformed out of shape.
Because it is the slot where the headgate for the milking stand fits into it, I can't use the headgate without that square pocket! Without the headgate to secure my fidgety first freshener, the stand is, at most, a nice platform with a ramp. I wouldn't be so mad if it was a square pocket for one of the side rails, but yea, no, it had to be the headgate.
The UPS driver delivered the package very carefully. The man listened to the directions to lay the package flat with the marked side up (I was there to receive it personally). I transported it by sled, flat with that marked side up, to the tractor shed. I only unboxed it today (got it this past Thursday, but I was busy until now). Now I am kicking myself. I already cut apart the box, too, which was a derp move.
How can I fix this? How can I make it functional? What should I tell the seller? I am trying not to compose a "thanks for the crap" email. I will have to cool off a bit. I bought this stand because it was made in the U.S.A., and had good reviews backing it up. The seller did take much longer than originally estimated to ship to to me, but if orders are busy, they I can understand.
Last edited: